The Role of Automation in Optimizing Utility Work Management Software
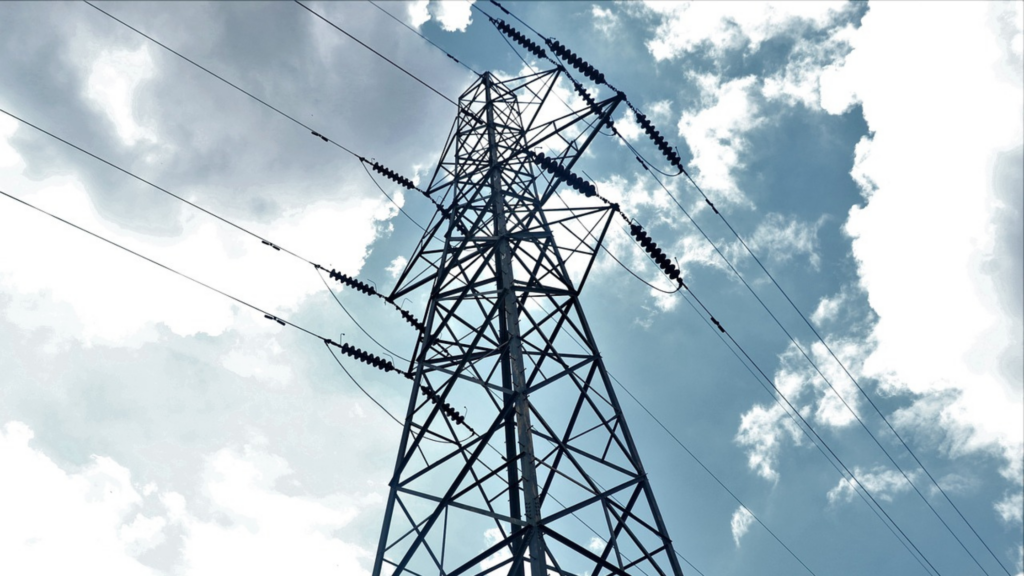
From false truck rolls to job delays, work management inefficiencies can significantly drive up the maintenance costs for transmission and distribution (T&D) companies. This, combined with inconsistent and cumbersome work management processes, can also result in frustrated teams, and even impact the overall stability of the power grid.
Because of this, it’s important to focus on optimizing efficiency and productivity for work management. Reports show that there will be a tripling of electricity demand by 2050. Utilities companies will need to focus on how to meet this increasing demand.
To get there, it starts at the core of work management, which includes:
- Understanding resource availability and allocating accordingly
- Scheduling (and adjusting) work based on priorities
- Providing information to support job requirements
Luckily, solutions that augment today’s utility work management software makes it easier than ever for asset management leaders in T&D to streamline resource allocation. In this blog post, see the top features that help to optimize T&D scheduling for maintenance teams.
Crew Availability in One View
Today, teams rely on various methods for tracking who is available for work. There may be a reliance on using email calendars or spreadsheets. If they do use a system of record for this information, it may not be kept up to date. This is often a cumbersome process to do so.
No matter which method may be used, it’s rare that all required information lives in one place. This can add to confusion and lack of visibility into who’s available to work, and when.
And, as the industry continue to change, technology will need to be a single source of truth for resource availability. The shifting workforce in the utilities industry, for instance, requires a bigger focus on training, mentorship, and development. This means that scheduling becomes a bigger challenge with crews spending time on the job outside of work sites.
To accommodate, it requires a faster and more efficient approach to accessing the data available in utility work management software. Using a low-code process automation tool that layers on top of the work management system can help solve this challenge. These tools seamlessly integrate with the core system to leverage the required data to optimize schedules, assignments, and priorities.
Because they feature easy-to-use interfaces and intuitive functionality, users can quickly make updates. Tracking resource availability, for instance, can be done in this external tool. If changes are made, they can be seamlessly communicated back to the system of record. This avoids the creation of a disparate source of information. (After all, the one thing that’s consistent in utilities asset management? Change.)
Clear Visibility Informs Scheduling
Balancing competing work priorities with resource capabilities makes scheduling crews a giant game of Tetris – and most of the time, it doesn’t feel as fun as the puzzle.
Prioritizing work, directing crews, and responding to outages means that field supervisors and managers require extensive visibility into work schedules and assignments. To add to the challenge, managers are often located hours away from crews – and may not have access to phone or internet service. This means it can be difficult to know which jobs to prioritize and how long they will take to complete.
And, for the manager scheduling and managing a disparate team, the ability to get this visibility across resources serves as paramount for several reasons, including:
- Identifying key priorities. Know what’s being worked on and why. This includes the ability to easily reschedule jobs based on changing priorities
- Getting real-time status updates to know where teams are working, how long jobs are taking, and see key challenges
- Consolidating scheduling events for a single view. This makes it easier to manage jobs and help stay in tune with team member priorities
This is where a process automation tool integrated with the core work management system can provide essential insight. Having a tool that pulls the most up-to-date information related to availability, priorities, and assignments can better inform work scheduling.
And, this work scheduling can be more efficient. In fact, recent data shows that using advanced technology to power smart scheduling can boost productivity by as much as 30 percent.
An all-in-one process automation tool uses data around job priorities, skill requirements, and other defined characteristics to leverages artificial intelligence (AI). It can generate hourly maintenance schedules to optimize workforce efficiency.
This technology leverages data science. In doing so, it can accommodate large backlogs of work. This isn’t all! It can also create smart schedules that consider other key priorities for team members, like training and development.
The result? An optimized schedule based on crew dynamics. Identifying crew locations becomes easier. And, teams clearly see what work will be completed on which days.
Easy Access to Job-related Information
A McKinsey report found that crews only spend about half of their time working at job sites. Traveling, training, and unassigned work account for the rest of the time. But, with automated and optimized schedules with the use of a scheduling software, their time on job sites could increase by more than 20 percent.
Part of this comes from having access to the information required to complete their jobs. For some crews, they may arrive to a job site to find the resources they require aren’t available – or that they didn’t bring it with them. In some cases, getting the tools or materials can cause significant delays.
Crews get a quick rundown of what’s on the schedule for the day via mobile access or daily emails within the software. This may include necessary resources to complete the assigned jobs. This can keep them informed and reduce the chances of them coming to the site without what they need.
Plus, the software stores a library rich in job-related details. As a result, teams can share their institutional information related to jobs, too. This may include:
- Detailed instructions for preventative maintenance requests that are completed infrequently or require expert insight
- Training videos for complex maintenance requests to support newer technicians
- Institutional knowledge for procedures or processes
Utility Work Management Software: The Future Starts with Automation
Emergent issues will always arise for T&D utilities, especially given challenges with aging infrastructure. Automation tools offer unmatched flexibility. After all, they empower organizations to quickly deploy crews to areas where they are needed most.
Leveraging Endevor’s automated scheduling technology on top of utility work management systems to optimize the work schedule can eliminate manual efforts and drive productivity.
This is just one area where technology can play a pivotal role for the T&D industry, and we’ll continue to see this evolve. Over the next decade, technologies will continue to shift to meet the changing demands of the industry – and it’ll require companies to focus on working with utility work management software that integrates it within the capabilities to align with key organizational priorities.
Interested in seeing how ENGAGE can simplify your scheduling and optimize work? Contact us for a demo.